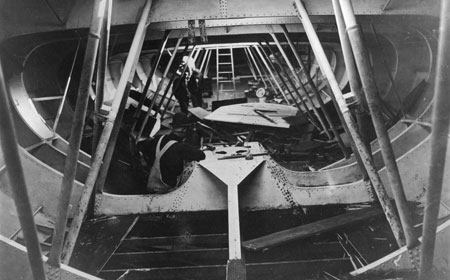
WOOD — A historically popular material for
shipbuilding because it was buoyant, widely available, and easily worked. However,
wood deteriorates easily. The common types of wood used in shipbuilding include
teak, cedar, oak, and pine.
BRONZE — A man-made alloy (mixture) of copper
and tin, and sometimes other metallic elements. Bronze is less brittle than iron and
is easily shaped. Throughout history, it was used in shipbuilding because of
its toughness and resistance to salt water corrosion. Bronze can still be found
in propellers and submerged bearings.
STEEL — A precise alloy (mixture) of iron,
carbon, and other natural metals. It is stronger than iron and wood, which protects
vessels from damage but is also heavier (about 30% heavier than aluminum). Steel
rusts unless protected from water, which often requires a finish, or a coating of
another material like zinc.
Vessels are designed with several steel grades and shapes: a complex steel structure
that meets requirements for cost, strength, flexibility, weldability, reparability,
etc.
The steel shapes in ships include plates, strips, bars, rods, tubular products,
and more. The steel grades in ships include HSLA (high-strength, low alloy), thermos
mechanical control process steels, anti-corrosion steels (oil tankers), clad plate
steels (chemical tankers), stainless steels, and more.
ALUMINUM — A natural metallic element that
becomes a silvery-white metal when refined. Aluminum is used in sheets for hulls or
for isolated structural members. It is
the lightest material for building large boats and easy to cut, but is difficult to weld and is very expensive. Corrosion is
also a concern with aluminum.
FIBERGLASS — Glass-reinforced plastic.
It is easily molded but must be reinforced with another material in order to provide
stiffness. Fiberglass hulls are largely free of corrosion.